Commercial Ice Machine Not Making Ice? Expert Troubleshooting and Solutions
For businesses in the hospitality and food service industries, a reliable ice supply is crucial. When your commercial ice machine stops making ice, it can disrupt operations and lead to unhappy customers. At Prime Genius Heating, Air & Appliances, we understand the importance of keeping your equipment running smoothly. In this blog post, we will delve into the common reasons why your commercial ice machine is not making ice and provide detailed solutions to get it back in working order. For expert assistance in the Greater Sacramento Area, call us at (916) 800-4007.
1. Inadequate Water Supply:
A constant and adequate water supply is essential for your commercial ice machine to function correctly. Ensure that the water line is not kinked, blocked, or frozen. A restricted water flow can prevent ice production. Over time, the water filter can become clogged with impurities. Replace the filter regularly to maintain a clean and sufficient water supply.
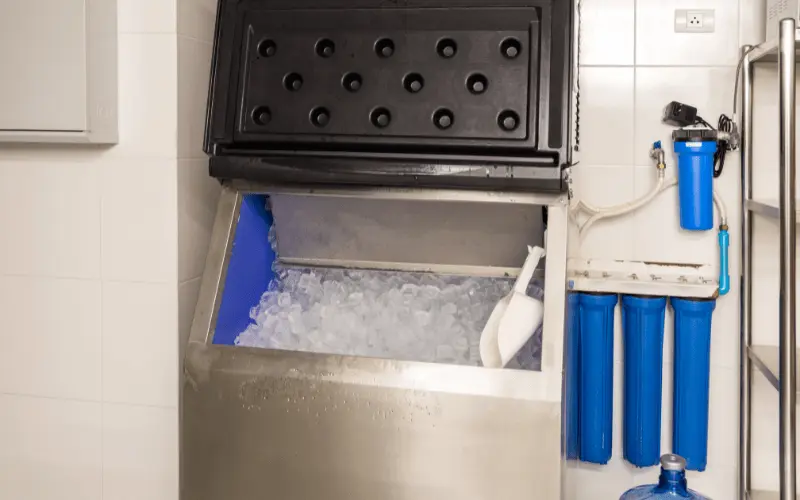
2. Faulty Water Inlet Valve:
The water inlet valve controls the flow of water into the ice maker. If it’s malfunctioning, the machine won’t get the necessary water to make ice. Using a multimeter, check if the valve is receiving power. If it is, but the valve isn’t opening, it may need to be replaced. Inspect the valve for any signs of leaks, which can hinder its functionality.
3. Temperature Issues:
Commercial ice machines rely on specific temperature ranges to produce ice efficiently. Temperature fluctuations can significantly affect performance. Ensure the thermostat is set to the recommended temperature. A thermostat that is set too high or too low can disrupt the ice-making process. Dirty condenser coils can cause the machine to overheat, affecting its ability to produce ice. Regularly clean these coils to prevent overheating.
4. Ice Maker Control Module Failure:
The control module manages the ice-making cycle. A faulty control module can stop the entire process. Sometimes, a simple reset can resolve issues with the control module. Refer to the manufacturer’s manual for specific reset instructions. If resetting doesn’t work, the control module may need to be replaced. Ensure you purchase the correct part for your machine model.
5. Clogged Ice Mold:
Ice molds can become clogged with mineral deposits or debris, preventing the machine from forming ice properly. Use a mixture of warm water and vinegar to clean the ice mold. Regular cleaning can prevent buildup and ensure smooth operation. Check the mold for any cracks or damage that could interfere with ice production.
6. Malfunctioning Ice Level Control Board:
The ice level control board monitors the ice bin’s fill level and signals the machine to stop or start making ice. A malfunctioning board can disrupt this cycle. Ensure the sensors are clean and unobstructed. Dust and debris can interfere with their operation. If the sensors are clean but the issue persists, the control board might need replacement.
7. Power Supply Issues:
A stable power supply is crucial for the proper operation of a commercial ice machine. Power interruptions can cause the machine to stop making ice. Ensure the circuit breaker is not tripped. Reset it if necessary. Look for any signs of damage or fraying in the power cord. A damaged cord can cause intermittent power issues.
Advanced Troubleshooting Techniques
1. Examine the Ice Production Cycle:
Understanding the ice production cycle can help diagnose issues more effectively. Pay attention to the sounds the machine makes during its cycle. Unusual noises can indicate specific problems, such as a faulty pump or motor. Ensure that the machine goes through both cycles correctly. Any interruption can indicate a problem with the control board or sensors.
2. Check for Software Updates:
Some modern ice machines come with software that may require updates. Refer to the manufacturer’s manual for instructions on checking and updating the software. If unsure, contact the manufacturer’s support team for guidance on updates and potential software-related issues.
3. Inspect the Bin Thermostat:
The bin thermostat controls the ice-making process based on the ice level in the bin. Use a multimeter to check if the thermostat is functioning correctly. A faulty bin thermostat can cause the machine to stop making ice prematurely. Ensure the settings are correctly adjusted according to the manufacturer’s recommendations.
Preventative Maintenance Tips
1. Regular Maintenance:
Regular maintenance is essential for the longevity and efficiency of your commercial ice machine. Follow the manufacturer’s recommended cleaning schedule. Regular cleaning prevents buildup and ensures optimal performance. Consider hiring a professional technician for annual servicing. They can identify and fix potential issues before they become major problems.
2. Proper Installation:
Proper installation ensures your ice machine operates efficiently from the start. Ensure the machine is level to prevent water flow issues and ensure even ice production. Install the machine in a well-ventilated area to prevent overheating. Overheating can severely affect the machine’s performance.
3. Use Quality Water:
The quality of water used can significantly impact the performance of your ice machine. If you have hard water, consider installing a water softener. Hard water can lead to mineral buildup, affecting ice production. Replace water filters as recommended by the manufacturer to ensure a clean water supply.
When to Call a Professional
While troubleshooting and minor repairs can often resolve issues, some problems require professional expertise. If you suspect electrical problems beyond a simple reset or inspection, call a professional technician. If the machine continues to malfunction despite following troubleshooting steps, professional diagnosis and repair may be necessary. If your machine is under warranty, unauthorized repairs can void the warranty. Always check warranty terms before attempting repairs.
Prime Genius Heating, Air & Appliances Services
At Prime Genius Heating, Air & Appliances, we offer expert repair and maintenance services for commercial ice machines in the Greater Sacramento Area. Our team of experienced technicians is equipped to handle a wide range of issues, ensuring minimal downtime for your business. We provide thorough diagnostics to identify the root cause of your ice machine issues. Our technicians carry a wide range of spare parts to perform efficient on-site repairs. Regular maintenance services keep your ice machine in top condition and prevent future breakdowns. For professional assistance, call us at (916) 800-4007. We are committed to keeping your business running smoothly with reliable ice production.
A commercial ice machine not making ice can be a significant disruption to your business operations. By understanding common issues and implementing proper maintenance and troubleshooting practices, you can minimize downtime and ensure a steady supply of ice. Regular cleaning, proper installation, and the use of quality water are key factors in maintaining your ice machine’s performance. When in doubt, don’t hesitate to call a professional to get your machine back in working order quickly. For expert help, contact Prime Genius Heating, Air & Appliances at (916) 800-4007, servicing the Greater Sacramento Area.